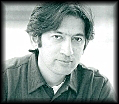
Editor's Ramblings
Manufacturing Execution Systems Allow for Innovation and Manage Variability
by
Naeem Ismat (Guest Contributor)
|
July, 2019
Few MES solutions have an advanced parametric configurator allowing users to build parts and products that have full parametric capabilities. To increase lean productivity and profitability, complex parts and products with unlimited variations must be represented by a single item. In a traditional MES system, variations could mean that more than 1.9 million different part numbers might be created to represent the different variations possible for a simple parametric box. Choosing a particular parameter not only changes the bill of materials, but also the bill of labor and the labor routings.
In a custom, one-of-a-kind manufacturing environment, the ability to estimate and configure items quickly and accurately rests on deliverables that are presented parametrically. The ability to estimate by the component or to use traditional methods, such as the lineal foot, is essential, especially when building a catalog of standard parts and products. Quickly providing comprehensive alternative proposals with price breakouts allows customer manufacturing shops to avoid ballpark guesses by giving them data and information to back up estimates. To meet project management requirements, it is important to schedule projects against existing production, while keeping track of changes through a comprehensive change-order process. This also affects a manufacturer's ability to manage total project costs versus budgeted. Material Management and Inventory Project-based manufacturing demands that MES solutions have the technological ability to purchase raw material to inventory or to a project and maintain perpetual inventory of raw materials. Likewise, the system should have the capacity to maintain and issue inventory in multiple units of measure within one inventory item, maintain inventory of value-added parts or finished products, and easily convert normally manufactured items to buyout items (adjusting the bill of labor and the bill of materials automatically). Still, these capabilities are rarely found in MES solutions. Other material management data that is quite helpful includes the ability to track highs, lows, vendor history, and serialized inventory.
Industry best practices require multiple checks during purchase order reconciliation. MES solutions are designed to improve business results by showing the user where costs are incurred, resulting in better cost-control and cost-reduction. Ideally the MES will drive increased capacity and sales. A well-tailored MES will empower the workforce by delivering information that motivates staff to make informed decisions supported by metrics. Effective project-based MES systems are designed to collect data at the point of transaction, eliminating duplicate data entry, and making the information available in real time.
Other demands, including compliance requirements, and internal and external collaboration are driving the need for data accessibility. Data accessibility must include a common set of numbers, historical views, and improved analysis. Internal and external employees all require access to the same data. Flexibility in accessibility and speed to communicate easily is critical with multiple locations. Multiple locations, time zones, currencies, and languages are the norm for many complex manufacturers, placing additional communication challenges on the organization. Innovation by its very nature induces variability. Manufacturing execution systems provide a framework for enabling rapid change due to innovation, while simultaneously managing risk, ensuring product quality, enforcing the adoption of new processes and maximizing production yields. Real-time parametric process and product analytical data must be used for continuous improvement of both product and process design.