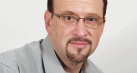
Why ISO 9001 is Still Relevant for Industrial Automation
by Thomas R. Cutler | July, 2010
Manufacturing Insights
Automation, Control & Plant Intelligence - Articles, Analysis, Reviews, Interviews & Views
by Thomas R. Cutler | July, 2010
Manufacturing Insights
YOU MAY LIKE:
Popular Articles
Manufacturing Insights