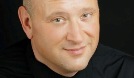
Compliance for Dairy and Food Processing Leads to Lean Automation Advancements
by Thomas R. Cutler | January, 2007
Manufacturing Insights
Automation, Control & Plant Intelligence - Articles, Analysis, Reviews, Interviews & Views
by Thomas R. Cutler | January, 2007
Manufacturing Insights
January, 2007, The Department of Homeland Security often suggests that the nation’s dairy supply
may be a target for future terrorism.
The results is a
need for technology solutions which provide real-time operations intelligence to
provide dairy processing plant management and staff with visibility of product
loss, wasted energy, or other inefficiencies, allowing them to take timely
corrective actions. According to Robert Moore, CEO of Vigilistics, a leading
diary technology provider, “It’s critical that technology solutions gather
information, provide analysis, notifications and reports, and communicates to
plant management.”
Complete
production tracking, initially for Bioterrorism Act and FDA compliance, is where
solutions, like Vigilistics started. Tracking of all product flows, all
equipment uses, CIP and other non-production as well as production modes, and
all possible co-mingling of products or contaminants is core to the
functionality of safety and automation in the dairy industry.
The complete
tracking capability led to other uses. Milk loss, for example, is a
significant cost for the dairy industry. Most losses are small amounts lost
during events such as loading or changeovers; most losses are due to correctable
human errors or inattention, or to operating procedures that can be improved.
But these loss events are masked by normal plant accounting. Technology tracking
capabilities proved useful in tracking product loss events, correlating to
persons, procedures, or equipment responsible, leading to reductions in product
losses of typically 50% or more, which is often greater than a million dollars a
year.
Tracking
equipment utilization as well as product flows is vital in automation
cost-savings. The details of energy
use during equipment modes, such as the non-production modes
of pasteurizers, evaporators, and dryers can waste considerable energy,
depending on the operating procedures.
These
software solutions fundamentally assemble data, correlated to production, and
provides analysis and tools to give plant management real-time visibility of
operations and the capability to make and enforce improvements.
The most
important point about the model-based data collection is that the resulting data
records are correlated to production, allowing efficient and flexible use of the
data.
Another
early step is the assessment of the Standard Reports vs. the plant
needs, and definition of any Custom
Reports. Also the intelligent rules for plant Notifications and
operator/shift Report Cards
can be set at this stage.
Examples of
available reports include:
Receiving
– the
starting point for genealogy and product history tracking. Accurate records of
receiving and analysis of variances generally leads to significant economic
return.
Fluid
processing –
pasteurization, separation and standardization – including product tracking and
real-time notifications of problems.
Batch
processing operations
for cheese, ice cream, cultured products – including electronic batch records
(make sheets) and analysis of efficiencies and material use. Product history
reports keep track of correlated data about ingredients, equipment used and
processing conditions, providing a basis for yield and quality analysis.
Filling and
packaging operations,
including downtime and efficiency analysis.
Plant Manager: Supplying
automatic notifications by e-mail, with attached reports, on variances beyond
chosen limits on any measured or analyzed quantity. The same is available for
any periodic report. A plant manager may not want the detailed report on plant
receiving, but if a significant variance is analyzed, the manager may want
notification and a report. The software can detect even small variances between
milk receipts and farm tickets. The individual variances can be small, and may
cancel out in most cases, but an analysis and correlation may show the largest
causes of losses over multiple deliveries.
Plant Engineer/Plant Analyst: Notifications and reports are available for plant
technical staff, just as for managers. Generally the staff may have different
intelligent rules triggering the real-time notifications, and they may have more
detailed reports. An analyst looked at data for a dryer, and produced the
following analysis of energy use during non-production modes. The analysis
showed clearly the days when excessive energy was used, and this was traced to
specific operator behavior. The operators were given better guidelines, and the
problem events were eliminated. The savings was about 3% of plant energy costs.
Note that notifications could be defined for events like excessive energy use.
Other Plant Staff:
Specific
reports are useful for other plant staff. CIP reports have been accepted by the
FDA in some cases as replacements for chart recorders. The CIP reports and other
reports on pasteurization and tank storage are of interest to plant quality
control. Reports on production data, real-time inventories and cost data are
useful for plant accounting.
While the
Bioterrorism Act may have driven the need for many of the new technology
solutions, the benefits far exceed lot traceability. The ability to monitor and track these
data is simply better business for the dairy industry.
Thomas R. Cutler is the President & CEO of Fort Lauderdale, Florida-based TR Cutler, Inc., the largest manufacturing marketing firm worldwide – www.trcutlerinc.com. Cutler is the founder of the Manufacturing Media Consortium of twenty seven hundred journalists and editors writing about trends in manufacturing. Cutler is also the author of the Manufacturers’ Public Relations and Media Guide. Cutler is a frequently published author within the manufacturing sector with more than 300 feature articles authored annually; he can be contacted at trcutler@trcutlerinc.com.
YOU MAY LIKE:
Popular Articles
Manufacturing Insights