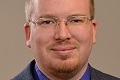
Best-in-Class Engineer-to-Order ERP Automates Custom Manufacturing
by Andrew Schutte | August, 2020
SaaS | Internet of Things | Manufacturing | Sensors
Automation, Control & Plant Intelligence - Articles, Analysis, Reviews, Interviews & Views
by Andrew Schutte | August, 2020
SaaS | Internet of Things | Manufacturing | Sensors
YOU MAY LIKE:
Popular Articles
Manufacturing Insights