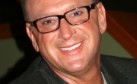
Improved Productivity and Throughput Jumps With Integrated Conveyor System Combined with Paperless Picking and WMS
by Thomas R. Cutler | June 15, 2016
Automation, Control & Plant Intelligence - Articles, Analysis, Reviews, Interviews & Views
by Thomas R. Cutler | June 15, 2016
YOU MAY LIKE:
Popular Articles
Manufacturing Insights