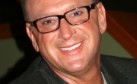
Distribution 2012: Hand Truck Efficiency Drives Supply Chain Solutions
by Thomas R. Cutler | January, 2012
Manufacturing Insights
Automation, Control & Plant Intelligence - Articles, Analysis, Reviews, Interviews & Views
by Thomas R. Cutler | January, 2012
Manufacturing Insights
YOU MAY LIKE:
Popular Articles
Manufacturing Insights