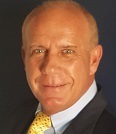
The Problem: ERP Systems Struggle to Synchronize ManufacturingThe Solution: Demand Driven Enterprise-wide Supply Chain Solutions
by Frank Kapper | Jan 11, 2018
Automation, Control & Plant Intelligence - Articles, Analysis, Reviews, Interviews & Views
by Frank Kapper | Jan 11, 2018
YOU MAY LIKE:
Popular Articles
Manufacturing Insights