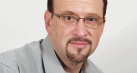
The Common Automation Denominator: Cimquest INGEAR
by Thomas R. Cutler | September, 2010
Manufacturing Insights
Automation, Control & Plant Intelligence - Articles, Analysis, Reviews, Interviews & Views
by Thomas R. Cutler | September, 2010
Manufacturing Insights
YOU MAY LIKE:
Popular Articles
Manufacturing Insights