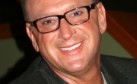
Autonomous Forklifts During the Pandemic : Automation as a Return-to-Work Strategy
by Thomas R. Cutler | July, 2020
Automation, Control & Plant Intelligence - Articles, Analysis, Reviews, Interviews & Views
by Thomas R. Cutler | July, 2020
Any manufacturer operating two or more forklifts currently, must consider replacing one unit with an autonomous forklift in 2020.
Simplicity is essential for small and midsized manufacturers purchasing their first autonomous forklift.
YOU MAY LIKE:
Popular Articles
Manufacturing Insights