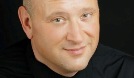
Molding and Extrusion Require Skilled Labor
by Thomas R. Cutler | March, 2007
Manufacturing Insights
Automation, Control & Plant Intelligence - Articles, Analysis, Reviews, Interviews & Views
by Thomas R. Cutler | March, 2007
Manufacturing Insights
Julie Maydew, vice president of ResourceMFG, the leading manufacturing placement organization detailed some of the core personnel challenges in the plastics sector. According to Maydew, “The plastics industry utilizes a wide variety of skills in its production units with emphasis on processes and equipment setup used to make the product. Molding and Extrusion cover a wide diversity of products and in order to find skilled personnel they must be recruited from other plastics industries. With the exception of entry level machine operators and secondary operations staff, molding and extruder specific experience are required; couple that with the variety of raw materials the profile for the ideal candidate is often unique to the hiring company. The matches must be made with candidates that have comparable process and material familiarity and experience.”
Since much of
the molding and extrusion has been sent offshore, the specific skills required
have migrated to other process industries and have
adapted outside of plastics manufacturing. With fewer production
facilities in the
Maydew insists that the plastics industry face unique
pressures from other sectors:
“Pressure from other process industries (primarily food, pharmaceutical,
hydrocarbon, and chemical production) has taken the Process Technicians,
Extruder/Molding Setup Operators and Maintenance Technicians away from the
dwindling
All process industries utilize maintenance mechanics and maintenance electricians along with skilled personnel that can readily change over the production equipment, the plastics industry has suffered as opportunities abound in the other segments.
Due to the placement segmentation ResourceMFG is involved with all aspects of manufacturing and is distinctly aligned with the skilled employees that are utilized within the plastics sector; the relationships with other process industries is used to transition highly skilled employees into plastics process operations. Through special partnering methodologies the firm is able to provide evaluations that are specific to each company.
A ResourceMFG plastics client illustrated the
capacity to address the sector. “We
provide precision plastic injection molding and extrusion employees to Sercel,
Inc. in
Globalization has deeply impacted the hiring
processes of plastic mfg plants in
Thomas R. Cutler is the President & CEO of Fort Lauderdale, Florida-based TR Cutler, Inc., the largest manufacturing marketing firm worldwide – www.trcutlerinc.com. Cutler is the founder of the Manufacturing Media Consortium of twenty seven hundred journalists and editors writing about trends in manufacturing. Cutler is also the author of the Manufacturers’ Public Relations and Media Guide. Cutler is a frequently published author within the manufacturing sector with more than 300 feature articles authored annually; he can be contacted at trcutler@trcutlerinc.com.
YOU MAY LIKE:
Popular Articles
Manufacturing Insights