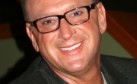
Automation Success Only Possible through Employee Engagement and Communication
by Thomas R. Cutler | July, 2014
Automation, Control & Plant Intelligence - Articles, Analysis, Reviews, Interviews & Views
by Thomas R. Cutler | July, 2014
YOU MAY LIKE:
Popular Articles
Manufacturing Insights